針對面板、晶圓、電路板檢測及大型書面掃描量身打造的全新感光元件技術
自從 1970 年代 CCD 影像感光技術萌芽以來,沒過幾年就發展出,或者說用於世界第一套 TDI 感光元件。TDI 感光元件由許多像素組成,現今最高解析度的款式,一條平行線約有 23k 畫素。物理意義上,它的像素總數為平行於長邊線上的像素個數,再乘以總共有幾條線,幾條線又稱作有幾個“stage”。那麼多的像素,它的工作原理是,先曝光一條線然後再曝光下一條線,每條線的資料會加總到下一條,直到全部的線都加總一遍,最後的結果就是所有線上的曝光都累積了一輪,所以整體感光度就是幾條線的總和。舉例來說,一個有 256 條線的 TDI,感光度就是 256 x 單條線的感光度。當然,這只是簡單的講法,實際情況比較複雜,感光度的累積會比理想低一點。至今現行的 TDI 感光元件有用 CCD 及 CMOS 兩種,兩種各有優缺點。
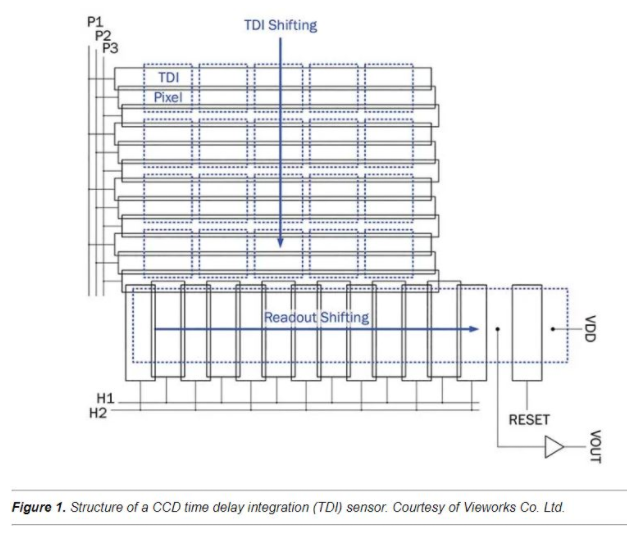
CMOS vs. CCD
CCD TDI 感光元件 (如上圖 Figure 1) 架構已經普及多年,簡單來說,最主要的優點在於,當進行曝光累積的時候只有電荷被搬動,這個過程幾乎不產生雜訊。意思就是說,當想要整合每個 CCD 上的圖素資訊,結果又想要維持既有的雜訊、動態範圍水準時,對 CCD 架構根本就是撿現成、家常便飯。也不是沒有缺點,這個例外就是,由於 TDI 通常用於極快的取樣頻率 (高速、短曝光) 場景及環境,CCD 結構天生在短曝光情況會有較高的暗雜訊。影像暗雜訊是暗電流造成,那甚麼是暗電流呢,因為熱,熱會影響感光元件,即使沒有光打在上面,它仍然會產生少許電子跑到附近的圖素上。
所以,CCD 主要的缺點是它用類比訊號輸出資料,因此需要在感光元件外增加額外的 A/D 類比轉數位 電路、水平及垂直驅動電路、訊號放大器。這些額外的設計增加了複雜度、增加成本,多出的元件增加發熱也增加了雜訊,然後耗電量也比較大。
CMOS 形式的 TDI 感光元件 (如上圖 Figure 2) 解決了 CCD 用類比輸出的諸多問題,因為在半導體晶片電路設計就直接將每個像素內做了自己的 A/D 類比轉數位轉換器,而不是在晶片外加其他的電路,此舉增加了資料傳輸速度,耗電量也遠低於 CCD TDI 感光元件。不過,再回到 TDI 這件事,TDI 累進曝光的過程中雖然累積了感光度,但 CMOS 架構因為有頻繁的 A/D 轉換,反而讓 TDI 同時也累積了雜訊。
有很多研究團體一直致力於改善這兩種科技的缺點,這幾年比較受人注目的是 Imec (愛美科) 於 2013 年發表的 Hybrid TDI (混合式 TDI) 感光元件展示品,簡單說就是把 CCD 藏在 CMOS 裡面。不過可惜,這個技術一直處於原型階段未被商品化。
經過數年的研發,到了 2016 年,第一款商用 Hybrid 感光元件終於亮相 (如上圖 Figure 3),整合 CCD 及 CMOS 的好處,剔除它們為人詬病的缺點。
Hybrid 混合式感光元件: 整合兩種領域的最佳方案
Hybrid 混合式感光元件設計能超過 90% 的感光填充係數 (fill factor : 單一畫素中可用於吸收光的面積占該畫素的比例。通常 CCD 可達 100%,但 CMOS 因為畫素旁有別的東西故遠低於這個數字)。用 CCD 當感光圖素,因為信噪比高、TDI 過程幾乎不產生多於雜訊,所以影像畫質較高;而 CMOS 結構在感光晶片上內嵌 A/D 類比轉數位可保證比較快的數位訊號讀取速度,降低晶片外額外複雜電路的成本,而且耗電量只有約 CCD TDI 的 25%。
為了打造混合式感光元件,原本 CMOS 製程中好幾個階段都要拆分出來,才能把 CCD 感光圖素嵌入到裡面去。最大挑戰是你又不能動到 CMOS 本身的特性條件,所以能動的地方很有限。為了克服挑戰,工程師們直接在半導體廠進行研究,實現針對 TDI 優化的 CCD,能達到電荷傳輸效率 99.99% 以上,以 110 nm 基線製程製作。
下一個重大挑戰則是在 CMOS 晶片加上一些類比電路設計,例如雙重關連式取樣電路 (Correlated Double Sampling / CDS 一種抑制雜訊的電路設計技巧),以及在 CCD 輸出端加入 A/D 類比轉數位電路 (如上圖 Figure 4)。既然 CCD 採用序列式 (排隊丟出來) 處理輸出資訊因此處理速度有一定的極限在,那麼就用 CMOS 這種平行處理的概念來改善設計。另一招則是用多工器(multiplexer / 一種可以從多個類比或數位輸入訊號中選擇一個訊號進行輸出的器件),將好幾組直行像素的輸出類比訊號綁在同一捆,丟給同一個 A/D 類比轉數位,這樣可以將像素排列得更緊湊。
然而,還是會擔心這些增加的額外電路設計可能還是會讓信噪比變差、耗電量增加,甚至會有固定的誤差雜訊 (fixed pattern noise / FPN),畢竟每個 A/D 類比數位轉換器都可能存在個體差異。在 Hybrid TDI用的雙重關連式取樣電路 (Correlated Double Sampling) 及針對每直行各有一組的 A/D 類比數位轉換等等,其實在 CMOS 影像感光元件已經很普遍、成熟,這些都已經可以達到高均質度、低功耗。
為了在狹窄的直行寬度內 (高畫素感光元件像素密度很高) 實現 12-bit 高效能的 A/D 類比數位轉換器,用了在 CMOS 的有限空間內將奇數行與偶數行的像素取樣分別往上下分區錯開的技巧。
因為 TDI 需要能雙向運作 (正掃描累積 / 反掃描累積),所以將 CCD 的訊號輸出單元設計成上下兩側都有,依照使用者設定選擇,訊號能自由切換到往上或往下的輸出單元上。以上種種設計讓 Hybrid TDI 感光元件像素密度可以壓縮到 3.5 μm 這麼小。
通常在半導體製程中,最大的晶片尺寸不會達到 32 mm 長,為打造一顆比這個長度還大的感光元件,會用到所謂的拼接 (stitching) 製程,製作整個 TDI 感光元件其實就是一直重複印製與感光元件中央區域相同的 pattern。
然而,原本這種拼接法只有 180 nm 製程能夠保證 pattern 銜接處的拼接連續性、均勻性。Vieworks 跟晶圓代工廠合作,成功在 110 nm 製程使用拼接工序,達到製程品質穩定;如此一來,就能用同一種光罩來生產各種不同尺寸的感光元件。
如圖 Figure 5,Hybrid TDI 技術跟其他家的 TDI 比起來感光度反應更好。這個感光度測試為求公平,特意用相同的畫素 (都是 12k x 256 stage)、系統 gain 值 (e-/DN) 以及影像位元深度,比較方法參照 EMVA1288 (歐洲機器視覺協會制定之相機測試標準),從圖中可以明顯看出 Hybrid TDI 優於一般的 CCD TDI 兩倍。其中,Hybrid TDI 的信噪比最高能達到 46 dB (200:1),而一般 CCD TDI 是44 dB (160:1);而動態範圍 Hybrid TDI 的 66 dB (2000:1) 高於 CCD TDI 的 57 dB (750:1);將 gain拉到最高時的暗雜訊水準,Hybrid TDI 只有 14 e- 優於 CCD TDI 的 33 e-。
自從導入 Hybrid TDI 技術,開發出從 3k / 32 stage / 7μm 一直到 23k / 256 stage / 3.5μm多種相機款式,線掃描速度最高可達 250 kHz (如圖 Figure 6)。這些劃時代的創新產品滿足客戶端對於高速、高感光的需求,拓展到市場應用。
這是一個用 Hybrid TDI line scan 相機所拍攝,針對 chip-on-film (COF) IC 封裝製程自動光學檢測的有趣範例,這種應用需要在非常細小的像素解析度達到低雜訊、高動態範圍。由韓國水原市 Warpvision 公司所開發的系統 (如圖 Figure 7),用 18k / 256 stage / 3.5μm 的 TDI 相機,在 3.5 倍放大倍率下,光學解析達到每個像素 1μm 的解析能力。此系統的開發帶有兩個目的,第一且直接的,就是檢測待測物上的電路是否正確 (如圖 Figure 8);第二,自動化光學檢測在解析度方面的能力提升,能夠帶動 chip-on-film IC 封裝製程往更精細的科技演進。
呼應主題,Hybrid TDI是一種破壞性的、創新研發科技,即將席捲面板、晶圓、電路板檢測及大型書面掃描應用市場。